The crazy weather has been up here in Houghton, MI for the past few days. Weather people said we were averaging 2-3 inches per hour the past day and a half. It finally let up a bit today. Still single digit temperatures and lots of blowing wind.
Over the past two days, every time I went out to shovel my houses driveway, it was knee deep again. Good thing it only takes me 5 minutes to walk to campus! You sure cant be out long when it is in the single digits and gusting around 30mph.
Thank goodness it is settling down now.
I mean, I love the snow, yes...but in nasty conditions, you can't even be out in it to enjoy it without getting frostbite.
Lots and lots of car accidents...people getting crunched and sliding off the road...or just not knowing where the heck the road even is.
If you ever visit Houghton, you will know how stupid steep the north south roads are. You can only imagine how hard driving can be. The only way most of us can get to our driveways from town is to take a couple mile long gradual sloping loop up towards the top of the hill, then come down the hill (many with grades exceeding 20 degrees) and hope you can make the turn into the driveway while coming down the hill. Not a change you can make it up those north south roads. It is hilarious to watch pickup trucks and jeeps try to make it up some of the hills. Cheap entertainment. But, who would have guessed that mini vans do pretty dog gone good! Makes you wonder how a bug would do for traction...hmmmm
Luckily, Houghton is really on top of snow removal. Much better than down state...say Holland, MI. hahaha, what a joke. The guys up here work around the clock. Every hour or two they come by and clear all the roads again. Main roads they use plow trucks. Side roads they use big Case or John Deere graders and front end loaders. When snow banks pile up to high, they scoop it up in front end loaders and truck it out and dump it away from civilization. Talk about burning a lot of diesel fuel. If the snow starts piling up to quick, they hook up the snow blowers to the front of the trucks to cut the shoulders wider until they can get more dump trucks to move snow away. It really is an amazing thing to watch when things ramp up. All hands on deck! They don't stop until the snow stops, because if they let it slide an hour or two, they won't be able to do a thing about it until the snow stops, which could take a couple days. For a town of less than 10,000 people, I would be willing to bet that Houghton has more snow removal equipment working around the clock than the entire City of Grand Rapids. If Holland were getting this snow, they would have had school closed for the past three days due to poor driving conditions. Up here they just take care of it as it comes and life goes on. Guess the difference between up here and Holland/Grand Rapids, where they seem to let it pile up while most the town is sleeping..
Salt doesn't do squat up here...it makes things so much worse. Sand is where it is at. It isn't at all like beach sand like Holland has. It is actually what they call Stamp Sand. It is all crushed up rock the many Copper Mine mills that dumped their tailings into the Portage, Torch lake, and Lake Superior. Miles of shoreline (some 800 acres of artificial land!!!) are nothing but crunchy tailings from the mines that nothing grows on because it is devoid of nutrients that plants need to grow. Hey, don't chya know, it makes good spread to throw down on the roads. Think of it like heavy cat litter that they throw everywhere. Thats a lot of cat litter!
Want to know why there is so much cat litter laying around up here???Time for another one of Dirk Van Appledorn's "Major American History that was never taught in our schools." Forgive me, I almost decided to be a history teacher before going into mechanical and industrial engineering

Michigan was home to the United States first major mineral rush. Unlike the slightly later California Gold "Bust" (lol), the copper rush in michigan actually amounted to something besides Chinese immigrants and a railroad connecting the east and the west. From 1843-1968, billions of dollars worth of copper was extracted from the ground. In todays money, the three companies to dominate the land (Calumet & Hecla, Copper Range, and Quincy Mining Company ) were each equivalent to the economic power house of General Electric. Quincy, the smallest of the three, built much of Boston Massachusetts in the late 1800's to the great depression by way of millions of dollars (in that time periods value...imagine what that would be today!!!) in dividends being payed out to eastern investors.
These hard rock underground workings extended to shaft depths of up to 9600 Feet, or just short of two miles into the ground! Temperatures near the surface were a cool 45 degrees year around. At the bottom as the shafts penatrated deep into the earths crust, temperatures typically were in the upper 90's. This is what a typical shaft house looked/looks like. Notice the size of the building compared to other houses around it.
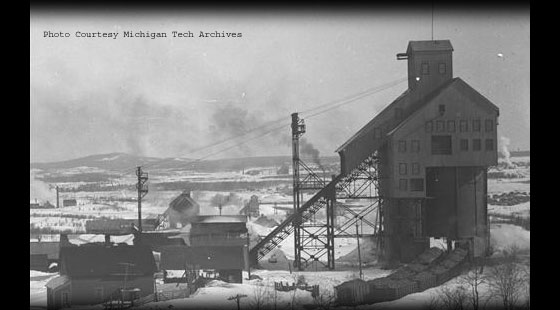
And below is the covering to a streamlined shaft that extended down 9600 feet into the ground...
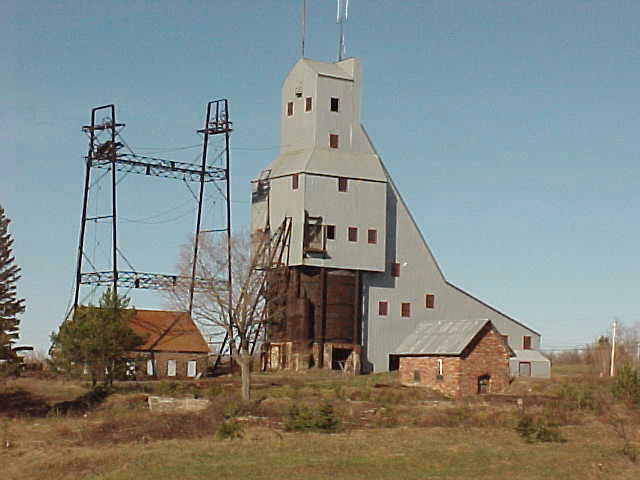
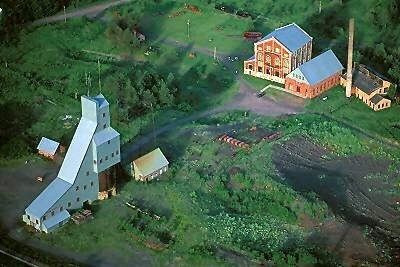
And here it is, the hoist that powered it, the Largest steam hoist in the WORLD, right across the portage from my house. I can look out the window and see the 5 story tall building it fills up on the hill top in Hanthingy. It was designed and build by the Nordburg MFG. Co. The steel forgings were so large that there was no American Iron works that could make such large parts. So, the main parts had to be made in Germany, then shipped here by boat. From 19teens to the early 1920's, Germany was the only country in the world capable of forging such massive stuff. This is the Quincy mines #2 hoist. It held some 13,000+ feet of hoisting cable. It could hoist 20,000lbs of ore at 36MPH. Talk about some serious power. Here it is in 1978...
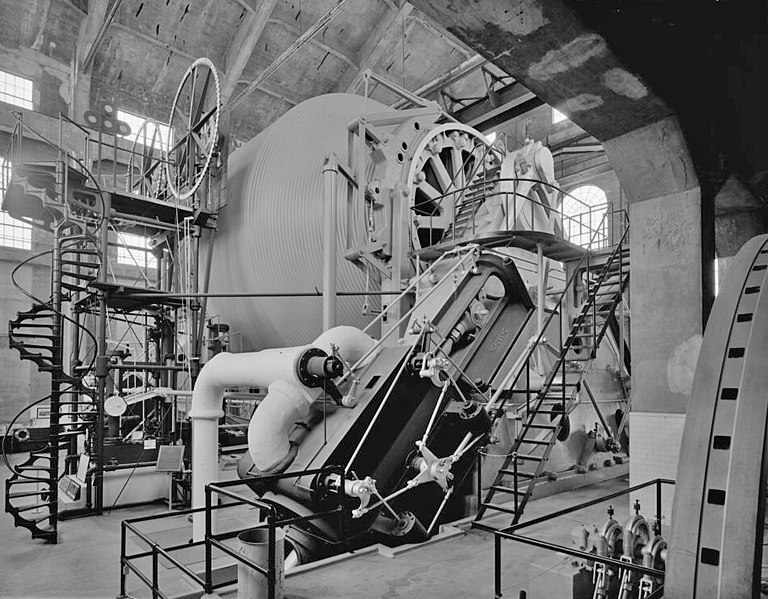
And here it is today...
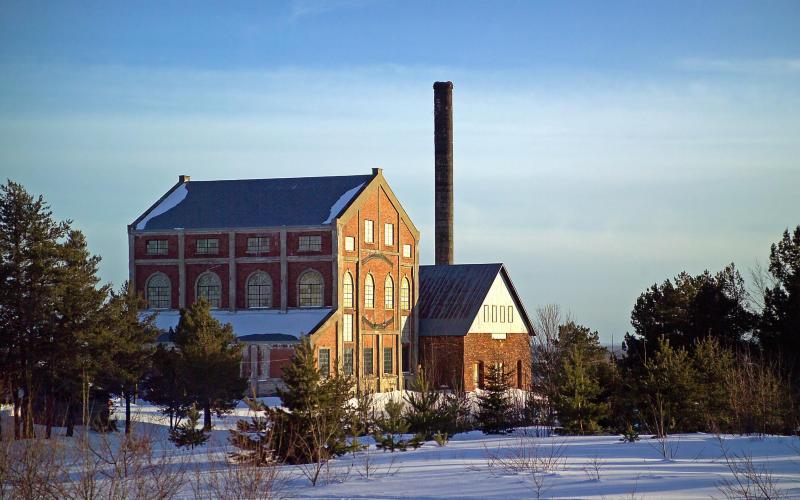

As you can imagine, the amount of material removed to make many mines this deep was astronomical. All this ore had to be crushed to liberate the sold copper from the rock. Yup, thats right, solid copper. Michigan is home to the worlds largest reserve of native copper. Native means it is in a solid form. While is some places of the world, one can find some small copper crystals the size of a small stone, Michigan had masses of copper the size of school busses. One of them extracted from the Minesota Mine (yes, one "N." Some dope in the 1800's misspelled Minnesota when creating the mine) was upwards to 50,000 Tons!!! As impressive as that is, it wasn't a big money maker. In fact, masses of copper were generally losers economicly. It took far to much man power to chisel up the mass because it could not be blasted into smaller pieces with high explosives. The mines that made money ignored the masses of copper, and went in search of fine flakes of copper evenly distributed among some rock layers. This was a much less labor intensive way of obtaining copper as much of the man power could be done by machine.
Enter, The Steam Stamp.
Stamps are an ancient technology employed at the local mines here in the mid 1800's. Large iron shoes were lifted by a cam and dropped repeatedly onto copper ore passing underneath until the particles were fine enough to be carried away by water to the rest of the mill. Watter carried the light rock away, and the heavy copper settled out. All the crush rock was discarded. These are early gravity stamps...

Milling technology evolved. Roller and cone crushers were introduced to the mining world. Unfortunately, the conglomerate and basalts of Michigan were so hard, that the new modern milling machinery would not hold up. Many attempts were made to solve this, but Michigan's stubborn flint hard rock of the Keweenaw peninsula would not allow it. So the only option left for the local mills was to beef up their stamps to make them higher capacity and more efficent. Decades of evolution produced the Steam Stamp. Gone were the revolving cams lifting and dropping iron shoes. Now massive steam cylinders reciprocated huge iron shoes weighing between 7000 to 8000 lbs, up and down over 100 times a minute, with strokes exceeding 24 inches. Massive foundations were needed to support the insane impact loads imparted by the steam stamps. The mills could now crush hundreds of tons of flint hard material every day. This mill was demolished in the mid 1970's. Over a dozen mills much like this one were operating in the copper country of Michigan...
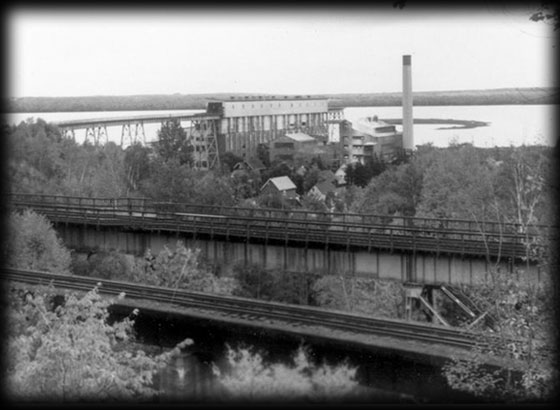
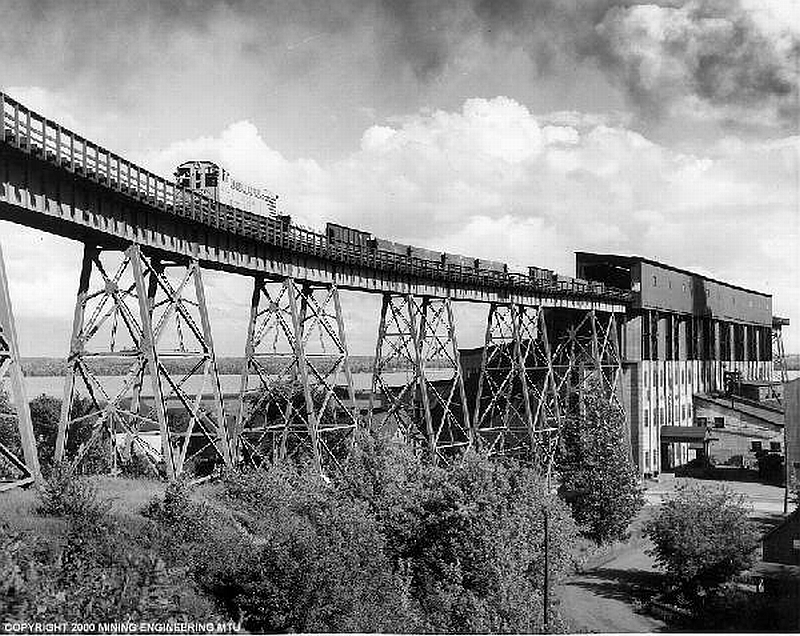
Below is one of only two of such monsters in existence today. One other like it was removed and relocated at a mining museum in Colorado. Yes, they were that unique....found nowhere else in the world, but Michigan. You can see in the photo the massive concrete foundations lined up where. This mill, the Ahmeek Mill (same as above) had eight of these. At one time during the peek of production in the 1920's, over 100 of these fire breathing monsters were in full operation along the Keweenaw Peninsula. I also included a diagram for you technical guys.


The blows would continue to pound the rocks into finer and finer grit. Once they were fine enough to pass though 5/16in mesh, the rock would be washed down to the separating floor of the mills by water. Lots of water. Each individual stamp would require millions of gallons of water each day to transport the crushed rock throughout the mill. Various methods of gravity separation were used to get as much of the fine flakes of copper. Only a few pound of copper flakes would be found in a ton of rock. Although it sounds small, that was the money maker. That just goes to show how horribly inefficient it was to try to chisel up large pieces of copper. In fact, many mines seeking this valuable rock with flakes of copper in simply tunneled around large masses of copper, leaving them in place when they encountered them underground.
So, if billions of pounds of copper were removed, and there were only a few pounds per ton of rock, then how much rock was removed? Lets not even go there. Let the pictures do the talking...








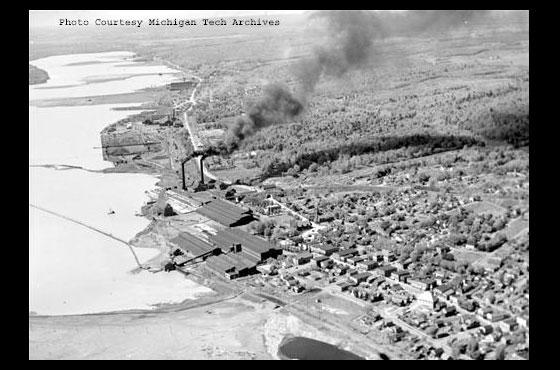
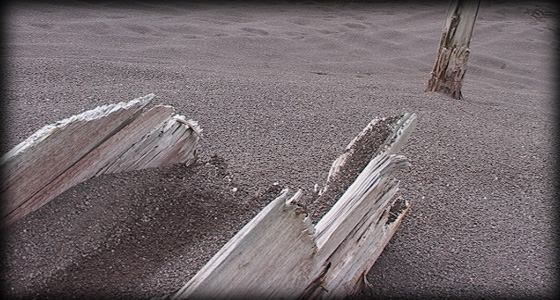

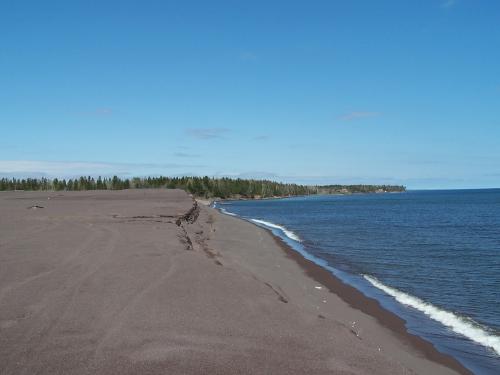




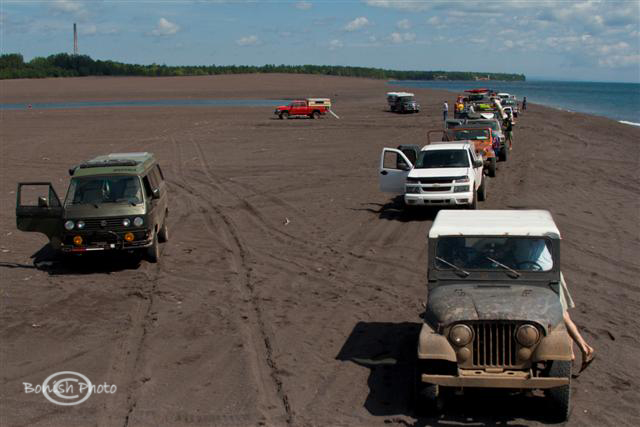

